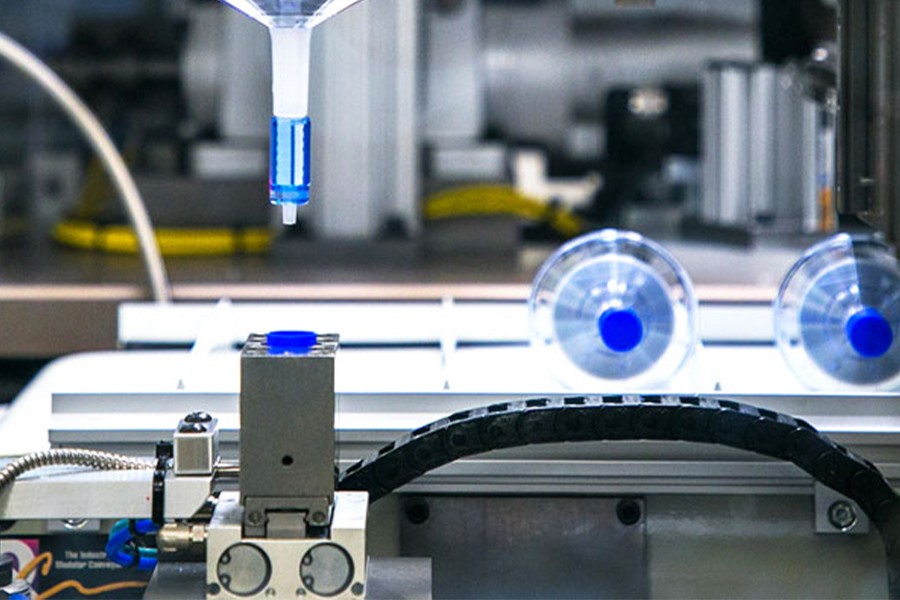
The machine in which the plastic injection process is carried out is called a plastic injection machine. American inventor John Wesley Hyatt, along with his brother Isaiah, patented the first injection molding machine in 1872. This machine was relatively simple compared to the machines in use today. It used a piston to inject plastic from a heated cylinder into the mold. The industry has progressed slowly over the years, producing products such as collar straps, buttons, and hair combs.
German chemists Arthur Eichengrün and Theodor Becker invented the first soluble forms of cellulose acetate in 1903, which were much less flammable than cellulose nitrate. In this way, a powder form that can be easily molded by injection was provided.
Arthur Eichengrün developed the first injection molding press in 1919 and patented injection molding of plasticized cellulose acetate in 1939.
Plastic injection machine basically consists of 4 main parts. These;
- Injection Unit
- Mold Unit
- Vise Unit
- Control unit
In cases where the plastic injection machine alone is not sufficient, additional auxiliary equipment is supported for the machine. The most important of the auxiliary equipment are:
- Hot runner control units
- Dryer and Dosing Systems
- They are conditioners
- Injection Unit
In this section of the plastic injection machine, granule or powder raw material is melted. This unit consists of funnel, screw, heaters, check-valve, injection nozzle, hydraulic cylinder and hydromotor.
The order of the raw material is provided by the funnel, which is transferred to the hive in one stream.
The screw, on the other hand, consists of 3 different parts where measuring, tightening and feeding operations are performed. In the measuring section, the ratio of the raw material transferred from the tower to the screw is determined, in compression, the raw material is melted at the desired degrees, and in feeding, the molten raw material is transferred to the mold.
The check valve is an apparatus attached to the end of the worm screw mechanism. This apparatus does not allow the molten raw material to flow back. It also allows the screw to act like a piston.