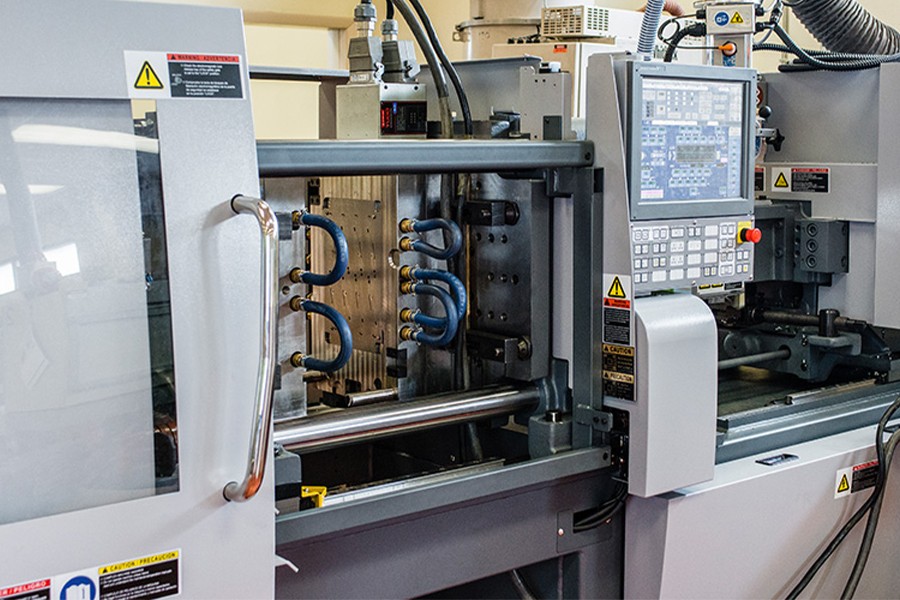
Plastic injection is basically the injection of plastic into a closed mold. rapidly from the runner inlet to the die chamber at high speed in a temperature range above the melt temperature. After injecting, the ironing phase and the holding phase and the tolerances of the dimensions and visuals of the part are acceptable. The principle of removing the plastic from the mold by bringing it below the demoulding temperature after It is a plastic part manufacturing method based on Since it is suitable for mass production, it is quite common in many sectors. It is a production method used. With this method, from the smallest components to automotive and defense industry products. Plastic parts can be manufactured in a wide variety of sizes and categories.
The advantages of plastic injection can be listed as follows;
- Low cost
- Compliance with automation
- No need for post-processing
- High speed production
- Compliance with the production of parts in different surfaces, colors and shapes
- Little material loss
- Production of different products in the same mold
- Able to work in low tolerances
Plastic injection is an uncomplicated method. The plastic injection method starts with connecting the mold to the plastic injection machine and feeding the granule or powder raw material into the hopper. Then the raw material is heated and transferred into the bucket where it will be melted. The molten raw material in the hive is passed through the nozzle under a certain pressure. Then, the melted raw material is transferred to the mold, which is colder than the barrel, under gradually changing pressure. In the meantime, the raw material is expected to cool for a certain time in the mold and the shaped product is taken from the mold by robot or by hand. After the product is received, the process starts again.